Прокатка – это обработка давлением, при которой исходная заготовка (слиток или отливка) под действием сил трения непрерывно втягивается между вращающимися валками и пластически деформируется с уменьшением толщины и увеличением длины, а иногда и ширины. Почти 90 % всей выплавляемой стали и значительная часть цветных металлов подвергается прокатке. В зависимости от формы и расположения валков и заготовок по отношению к ним различают продольную, поперечную и поперечно-винтовую прокатки.
При продольной прокатке (рис. 58) заготовка 1 деформируется между двумя валками 2, вращающимися в разные стороны, и перемещается в направлении, перпендикулярном осям валков.
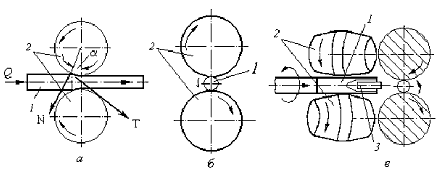 |
Рис. 58. Схема основных видов прокатки:
а) продольная; б) поперечная; в) поперечно-винтовая; Q – усилие прокатки;
N, T – нормальная и тангенциальная силы соответственно; ?– угол захвата;
1 – заготовка; 2 – валки; 3 – оправка |
При поперечной прокатке валки 2 вращаются в одном направлении, а заготовка 1, имеющая форму тела вращения, перемещается параллельно осям валков и обжимается по образующей с увеличением длины и уменьшением площади поперечного сечения.
При поперечно-винтовой прокатке валки 2 расположены под углом друг к другу, вращаются в одну сторону и при обжатии заготовки 1 сообщают ей вращательное и поступательное движения.
Если обозначить через ho, bo и lo соответственно толщину, ширину и длину исходной полосы, а через h1, b1 и l1 – конечной, то абсолютное обжатие:
Δh = h0 - h1;
соответственно абсолютное уширение
Δb = b1 - b0.
Величину деформации полосы при прокатке характеризуют следующие показатели (коэффициенты):
коэффициент обжатия
коэффициент вытяжки
Так как объём металла в процессе прокатки не меняется, то hobolo=h1b1l1 и
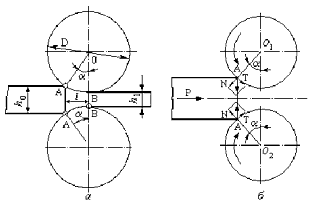 |
Рис. 59. Очаг деформации и угол захва-та при прокатке (а); схема действия сил
в момент захвата металла валками (б) |
P>Металл соприкасается с каждым из валков по дуге АВ (рис. 59), которую называют дугой захвата. Угол ?, соответствующий этой дуге, называется углом захвата.
Объём металла, ограниченный дугами захвата АВ, боковыми гранями полосы и плоскостями входа АА металла в валки и выхода ВВ металла из них, называют очагом деформации металла.
Процесс прокатки обеспечивается трением по контактным поверхностям валков с прокатываемой полосой. В момент захвата со стороны каждого валка на металл действуют две силы: нормальная N и тангециальная Т (сила трения). Известно, что
T = Nf,
где f – коэффициент трения.
Для осуществления захвата металла валками необходимо, чтобы соблюдалось условие f >tg?, т. е. тангенс угла захвата должен быть меньше коэффициента трения.
При горячей прокатке стали гладкими валками угол захвата равен 20–26о, при холодной 5–8о. Усилие прокатки P определяют по формуле: P=PсрF,
где Pср - среднее давление прокатки, F - горизонтальная проекция контактной площади металла с валком.
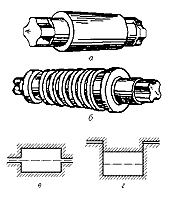 |
Рис. 60. Прокатные валки и калибры:
а) гладкий; б) с фигурными вырезами; в) калибр открытый; г) калибр закрытый |
Инструментом прокатки являются валки, которые могут быть не только гладкими (рис. 60), но и с фигурными вырезами – ручьями. Совокупность соответствующих вырезов в верхнем и нижнем валках образуют калибр. Калибры могут быть открытыми и закрыты-ми (рис. 60). Комплект прокатных валков со станиной называют рабочей клетью.
По числу и расположению валков в клетях, прокатные станы подразделяют на дуо-, трио-, кварто-, многовалковые и универсальные (рис. 61).
 |
Рис. 61. Рабочие клети прокатных станов:
а) дуо; б) трио; в) кварто; г) многовалковый; д) универсальные |
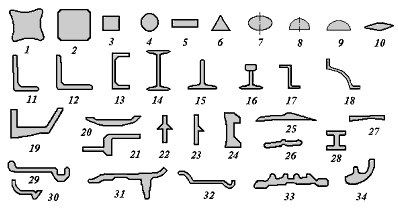 |
Рис. 62. Разновидности профилей проката:
1–10 – простые; 11–17 – фасонные; 18–34 – сложные специальные |
Форму поперечного сечения продукции, получаемой при прокатке, называют профи-лем. Совокупность форм и размеров профилей называют сортаментом. Сортамент прока-та подразделяется на группы: сортовой прокат, листовой, трубы и профили специального назначения (рис. 62).
В свою очередь, сортовой прокат по форме сечения разделяют на простой (круг, квадрат, шестигранник и др.) и фасонный (уголки, тавры и двутавры, рельсы, швеллеры и др.) Листовой прокат подразделяют на толстолистовой (4 мм и более) и тонколистовой (менее 4 мм).
Наиболее распространёнными видами проката являются блюмы, слябы и сортовой прокат.
Блюмы – заготовки квадратного сечения от 450 ? 450 до 150 ? 150 мм2, получаемые на блюминге в результате прокатки слитков, предварительно подогретых до 1 300 оС.
Слябы – заготовки прямоугольного сечения максимальной толщины до 350 мм и шириной до 2 300 мм, идущие для прокатки на толстый лист.
После прокатки на слябинге часть проката направляется на заготовочные станы. Полученные полосы режут на мерные куски необходимой длины – сутунки. Последующая обработка включает отделочные операции: зачистку, травление, удаление поверхностных дефектов. Полученные заготовки направляются на сортовые и листопрокатные станы. На сортовых станах заготовка после нагрева в печах последовательно проходит прокатку в 7–15 калибрах, в последнем из которых получают требуемый профиль (рис. 63).
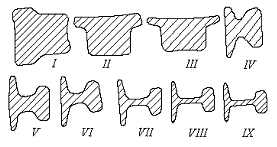 |
Рис. 63. Последовательность проката рельса на сортопрокатном стане |
Современная технология позволяет получать непрерывной холодной прокаткой листы толщиной менее 0,1 мм с суммарным обжатием до 80–90 % без промежуточной термической обработки.
Прокаткой освоено производство бесшовных и сварных труб как из стали, так и цветных металлов. Бесшовные изготовляют диаметром 30–650 мм с толщиной стенки от 2 до 160 мм, сварные – диаметром от 5 до 2 500 мм.
Возможно получение профилей специального назначения. Например, шары для подшипников, заготовки для шатунов, цельнокатаные вагонные колёса и др. |