В процессе затвердевания металлов и сплавов могут образовываться кристаллы различной формы, наиболее часто – разветвлённые, или древовидные, получившие название дендритов. Впервые они были обнаружены в затвердевшей стали русским металлургом Д.К. Черновым (1878). Дендриты образуются в процессе медленной кристаллизации из расплавов и паров. Их рост происходит главным образом в направлении плоскостей с максимальной плотностью упаковки атомов, т. е. с минимальным межатомным расстоянием. После возникновения зародыша начинает расти ось первого порядка – главная ось будущего дендритного кристалла. После этого перпендикулярно или под некоторым углом к ней растут оси второго порядка, перпендикулярно к ним – оси третьего порядка и т. д. При этом пространство между ветвями кристаллов и дендритами обогащается примесями, из-за затруднённого поступления в некоторые объёмы «питающей» жидкости при затвердевании образуются микропоры и микроскопические усадочные раковины, что ухудшает механические свойства материала. Так формируются неоднородные по химическому составу и структуре зёрна при кристаллизации, казалось бы, чистого металла. Схема дендритного кристалла приведена на рис. 16.
 |
Рис. 16. Схема дендритного кристалла:
I – ось первого порядка (главная ось);
II – ось второго порядка;
III – ось третьего порядка
|
При столкновении дендритов их правильная форма нарушается.
В случае кристаллизации сплавов неоднородность зёрен еще более усиливается, поскольку в ходе кристаллизации состав твёрдой фазы постоянно изменяется, не достигая при реальных скоростях охлаждения равновесного. Объёмы, затвердевшие в первую очередь, будут обогащены более тугоплавким компонентом. Сказанное можно легко представить после ознакомления с диаграммами состояния двойных сплавов (глава 5).
Формирование структуры слитка происходит в соответствии с рассмотренными выше закономерностями. Обычно в слитке можно выделить три зоны с различной структурой (рис. 17).
У поверхности холодной формы – изложницы – в слое сильно переохлаждённого жидкого металла формируется очень узкая зона относительно мелких равноосных (глобулярных) кристаллитов. Далее, к центру слитка, образуется зона из столбчатых зёрен – удлинённых дендритных кристаллитов, расположенных перпендикулярно к стенкам изложницы, т. е. в направлении отвода теплоты.
При сильном перегреве металла, высокой температуре литья, спокойном заполнении формы и быстром охлаждении зона удлинённых дендритных кристаллитов может заполнить весь объём отливки. Для столбчатой зоны характерны малое содержание раковин, газовых пузырей и высокая плотность. Однако по границам столбчатых зёрен металл имеет пониженную прочность, что может привести при последующей обработке давлением к возникновению трещин. Для стали, обладающей сравнительно невысокой пластичностью, развитие зоны столбчатых кристаллитов нежелательно, для пластичных материалов, например, меди и её сплавов, наоборот – желательно, поскольку разрушение слитка при обработке давлением не происходит, а сам слиток получается более плотным.
В случае низкой температуры литья и медленного охлаждения во внутренней части крупных отливок создаются условия для возникновения зародышей кристаллов. Это приводит к образованию зоны, состоящей из более или менее равноосных различно ориентированных в пространстве крупных зёрен. Возникновение кристаллов возможно еще в период литья вследствие охлаждения поверхности струи металла во время его заливки в форму. Попав в форму со струей, эти кристаллические зародыши могут расплавиться, а могут и сохраниться и вырасти в разветвлённые равноосные дендриты, мешающие росту столбчатых кристаллов.
Примеси, помимо общего измельчения зерна, изменяют соотношение столбчатой и равноосной зон, затрудняя линейный рост столбчатых кристаллов. При фасонном литье желательно получение мелкозернистой равноосной структуры.
Сопутствующий дефект макроструктуры отливок – усадочная раковина, образующаяся в той части, где затвердевание происходит в последнюю очередь. Усадочная раковина обычно окружена загрязнённой частью металла, пузырями, микро- и макропорами. Такой слиток нельзя использовать для получения изделий. Поэтому его верхнюю часть, 20–25 % металла по массе, отрезают и направляют на переплав.
В целом можно сказать, что для слитков, получаемых по традиционной схеме, характерны крупнозернистая, неоднородная структура, неравномерное распределение по сечению легирующих элементов и вредных примесей, неоднородность по химическому составу самих дендритов.
Указанные недостатки в значительной мере устраняются при получении слитков на установках непрерывной разливки стали. Её принципиальная схема приведена на рис. 18.
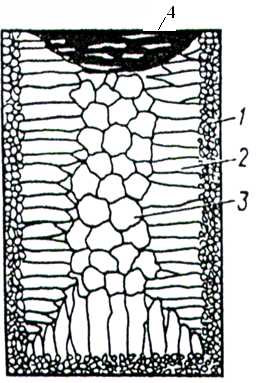 |
Рис. 17. Типичная макроструктура слитка:
1 – зона мелких равноосных кристаллов;
2 – зона столбчатых кристаллов, расположенных нормально к стенкам изложницы (формы);
3 – зона равноосных кристаллов больших размеров;
4 – усадочная раковина
|
 |
Рис. 18. Схема установки непрерывной разливки стали. Вертикальная разливка |
Жидкий расплав из ковша через разливочное устройство поступает в сквозную изложницу – кристаллизатор. Стенки кристаллизатора, изготовленные из меди, интенсивно охлаждаются водой. В начале работы шахту кристаллизатора перекрывают брусом-затравкой, который выполняет роль дна и искусственного центра кристаллизации. Затвердевший у стенок кристаллизатора и у поверхности бруса-затравки металл с определённой скоростью, составляющей обычно 0,5–1,5 м/мин, начинают извлекать из кристаллизатора, уровень металла в котором поддерживается постоянным.
Заготовка, выходящая из кристаллизатора, интенсивно орошается из форсунок водой, что приводит к получению мелкозернистой структуры. После затвердевания по всему сечению заготовка разрезается на части необходимой длины.
Способ непрерывной разливки стали повышает производительность и выход годного, обеспечивает большую степень однородности по длине и поперечному сечению заготовок, что, в свою очередь, повышает механические свойства и надёжность металлоизделий. Непрерывную разливку осуществляют в вертикальном и радиальном вариантах. |