1. Кинематические и геометрические параметры процесса резания
Обработка резанием – это процесс получения детали требуемой геометрической формы, размеров и шероховатости за счёт механического срезания с поверхностей заготовки материала технологического припуска в виде стружки. В зависимости от используемого типа инструмента способы механической обработки подразделяются на лезвийные и абразивные. Отличительной особенностью лезвийной обработки является наличие у обрабатывающего инструмента острой режущей кромки определённой геометрической формы, а для абразивной обработки – наличие различным образом ориентированных режущих зёрен абразивного инструмента, каждое из которых представляет микроклин.
К основным параметрам режима резания относятся скорость главного движения резания, скорость подачи и глубина резания. Скорость главного движения резания (скорость резания) определяется максимальной линейной скоростью главного движения режущей кромки инструмента (в м/с). При вращательном главном движении
где D – максимальный диаметр обрабатываемой поверхности заготовки, м;
? – угловая скорость, рад/с. При строгании и протягивании скорость резания ? определяется скоростью перемещения инструмента относительно заготовки. Подача инструмента определяется её скоростью s. Подача на один оборот S0 = us /n (при точении, сверлении и пр.). При строгании подача определяется на ход резца. Глубина резания h определяется расстоянием по нормали от обработанной поверхности заготовки до обрабатываемой (мм). Глубину резания задают на каждый рабочий ход инструмента. При точении цилиндрических поверхностей глубину резания определяют как полуразность диаметров до и после обработки:
где Dзаг – диаметр заготовки;
d – диаметр обработанной поверхности заготовки, мм.
Величины скорости резания, подачи и глубины резания определяют производительность и качество обрабатываемой поверхности. Геометрические параметры режущего инструмента определяются углами. Рассмотрим их на примере резца. На рис. 80 изображены координатные плоскости при точении и углы резца в статике:
· главный передний угол ? – угол между передней поверхностью лезвия и плоскостью, перпендикулярной к плоскости резания;
· главный задний угол ? – угол между задней поверхностью лезвия и плоскостью резания;
· угол заострения ? – угол между передней и задней поверхностями:

· угол наклона режущей кромки – угол в плоскости резания между режущей кром-кой и основной плоскостью.
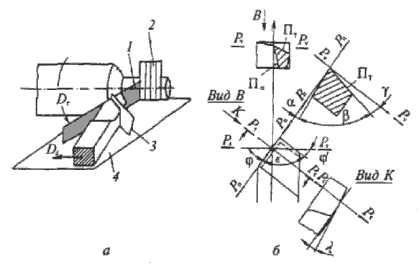 |
Рис. 80. Геометрические параметры токарного резца:
а) координатные плоскости; б) углы резца в статике;
1 – плоскость резания Рn; 2 – рабочая плоскость Рs; 3 – главная секущая плоскость Р?; 4 – основная плоскость Рv |
Углы в плане:
· главный угол в плане – угол в основной плоскости между следом плоскости резания и направлением продольной подачи;
· вспомогательный угол в плане ?? – угол в основной плоскости между вспомогательной режущей кромкой и обработанной поверхностью.
С увеличением угла ? инструмент легче врезается в материал, снижаются силы резания, улучшается качество поверхности, но повышается износ инструмента. Угол ? обеспечивает снижение трения инструмента о поверхность резания, уменьшая его износ, однако чрезмерное его увеличение приводит к ослаблению режущей кромки инструмента.
Силы резания представляют собой силы, действующие на режущий инструмент в процессе упругопластической деформации и разрушения срезаемой стружки. Их приводят к вершине лезвия или к точке режущей кромки и раскладывают по прямоугольным координатным осям. Расчёт усилия резания производят по эмпирическим формулам. Мощность процесса резания (кг?м/с определяется (упрощённо) произведением:
N = PV,
где P – усилие резания, кг;
V – скорость резания, м/с.
Производительность обработки при резании определяется числом деталей, изготовляемых в единицу времени:
Q = 1/Tшт.
Время изготовления одной детали Тшт:
Тшт = То + Тин + Твсп,
где То – машинное время обработки резанием;
Тин – время подвода и отвода инструмента;
Твсп – вспомогательное время установки и настройки.
Производительность обработки определяется машинным временем То. При токарной обработке:
То = La / (nSoh),
где L – расчётная длина хода резца, мм;
а – припуск на обработку, мм;
а/h – характеризует требуемое число проходов инструмента при обработке с глубиной резания hо.
Поэтому наибольшая производительность будет при обработке с глубиной резания
h = a,
наибольшей подачей Sо и максимальной скоростью резания. Однако при увеличении производительности снижается качество поверхности и повышается износ инструмента. |